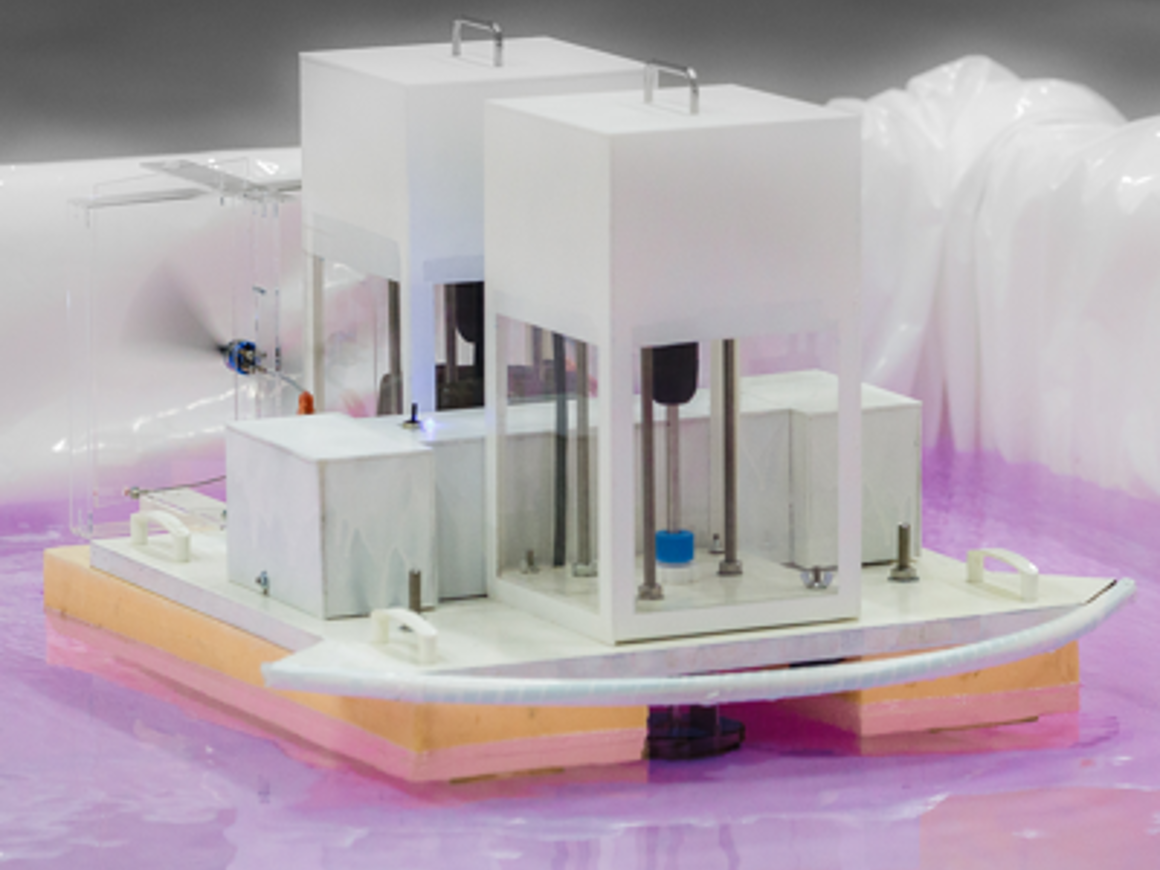
Remote controlled raft for treatment of large volumes of water
Industries that generate large quantities of liquid waste, e.g. the nuclear energy or mining industries, are familiar with the accumulation of water in ponds, both indoor and outdoor. The treatment of the water necessary for release can seem as an insurmountable challenge, both based on the sheer volume and on the hazards involved. Pumping the waste through a column would typically involve high pressure, while any accidental release or spillage must be avoided.