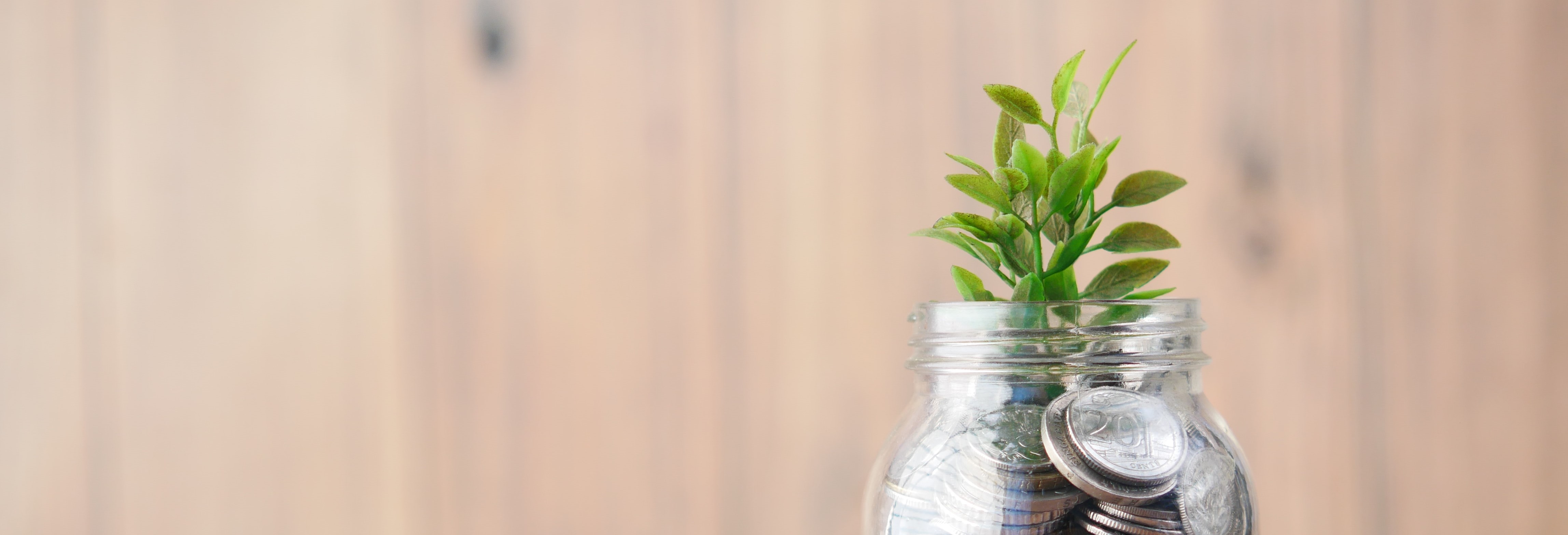
Struggling to Make Biocatalysis Pay Off?
The use of enzymes as catalysts allows to account for environmental concerns in chemical manufacturing: It comes with milder reaction conditions, lower temperatures, and can replace toxic chemical catalysts. However, the key hurdle is to make biocatalytic routes economically viable and profitable despite high up-front costs for the enzyme.
The Solution
Recycling and reusing the biocatalyst lowers output specific catalyst costs and thus boosts economic viability. Unfortunately, traditional impeller stirred reactors exert mechanical stresses onto the biocatalyst, which severely shortens its useful lifetime.
The rotating bed reactor (RBR) protects the immobilized enzymes by retaining them in a unique stirrer equipped with filters.
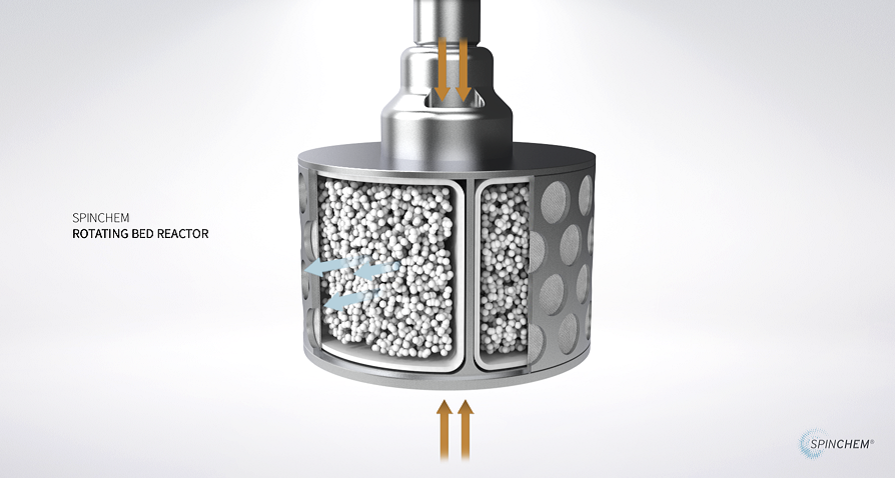
When rotated, the RBR generates a flow of liquid passing the enzymes at a rate superior to that of a column, while completely remediating the issues of attrition associated with a stirred tank reactor.
Learn more about the concept here.
Making an antiviral Covid-19 drug
The 'Medicines For All Institute' developed a route for manufacturing Molnupiravir, used for treating Covid-19. Enzyme expenses were high: 50% of the raw material cost. After implementing an RBR, they were able to conveniently reuse the biocatalyst for repeated batches with preserved performance.
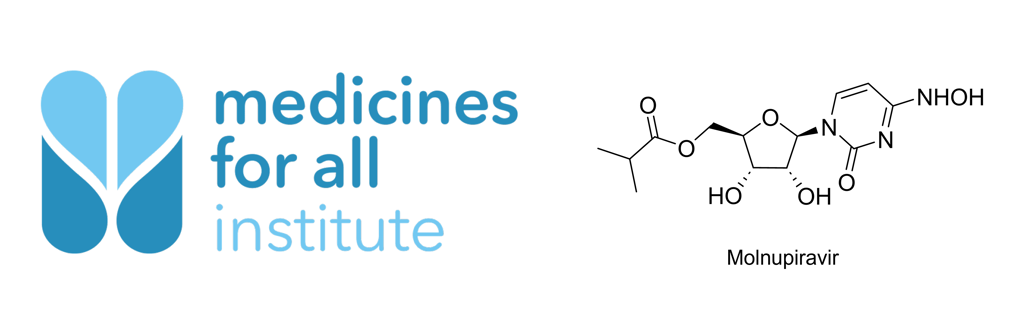
AstraZeneca scale up
AstraZeneca, one of the world's largest pharmaceutical companies, used an RBR to improve recycling of their immobilized enzyme. Published in Organic Process Research & Development, the authors note: “the immobilized enzyme was surprisingly stable ... and we could run 10 consecutive recycling experiments with preserved rate of reaction and enantioselectivity”.
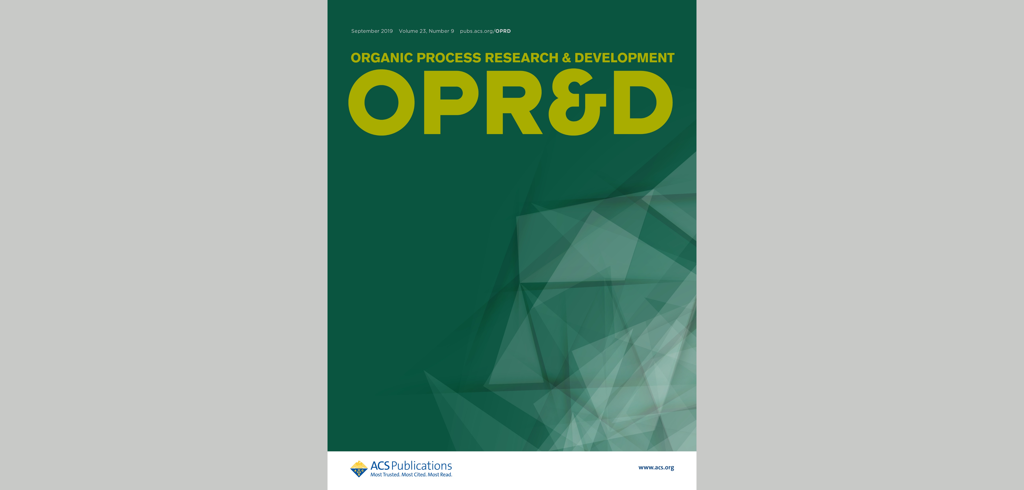
Hot API production
XP Chemistries AB is a producer of sustainable capsaicin, the molecule responsible for the "heat" in chili peppers. The ProRBR product range allowed XP Chemistries to smoothly transfer their well-developed reaction from the benchtop to 100 L scale. Today XP Chemistries are producing capsaicin at high volume and with unique purity, positioning them as the world leading producer of sustainable capsaicin.
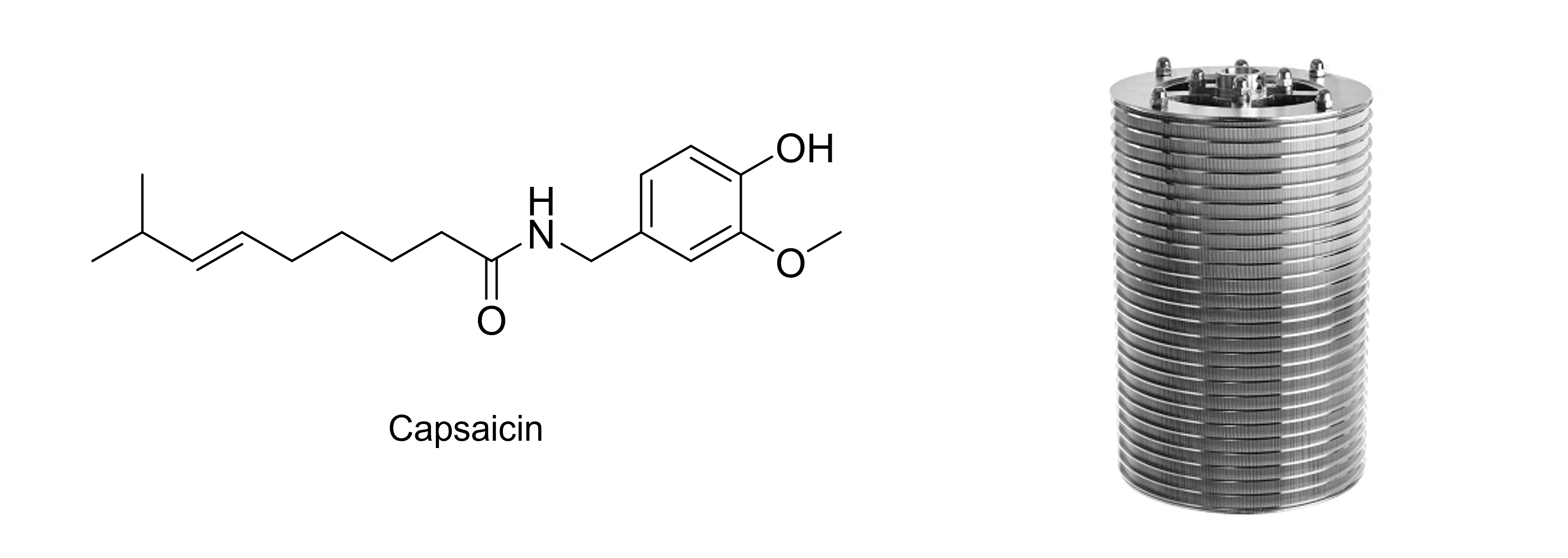
The impact of the rotating bed reactor
Researchers can now experiment without breaking the bank, process development scientists can reach the required purity and yield per kilogram of biocatalyst, and all chemists can contribute to a sustainable production of pharmaceuticals.
What is holding you back from a environmentally and economically sustainable process?