At SpinChem, our passion drives us to create innovative solutions that contribute to cleaner oceans and purer air. We believe that our technology can play a crucial role in addressing some of the most pressing environmental challenges of our time.
Our commitment to sustainability is reflected in our versatile SpinChem® rotating bed reactor, which finds applications across a wide range of industries. From water purification and toxic waste treatment to the production of renewable fuels, cosmetics, and pharmaceuticals, our technology is making a significant impact on both industrial processes and environmental conservation efforts.
By continuously pushing the boundaries of what's possible in synthesis, production, and purification, we strive to create a world where technological advancement goes hand in hand with environmental stewardship. Our goal is not just to innovate, but to innovate responsibly, always keeping in mind the health of our planet and its oceans.
Technology
The SpinChem® Rotating Bed Reactor (RBR) is at the heart of our innovative technology. This versatile device enhances mass transfer in heterogeneous reactions, significantly improving efficiency and productivity in various chemical processes.
Key features of the RBR include:
- High mass transfer rates due to forced convection
- Flexible design allowing for easy scale-up
- Reduced processing times compared to traditional methods
- Improved product quality and yield
The RBR's unique design makes it particularly effective in applications such as catalysis, ion exchange, and adsorption, enabling more sustainable and efficient industrial processes across multiple sectors.
The SpinChem® Rotating Bed Reactor (RBR) operates on a simple yet powerful principle:
- The reactor consists of a cylindrical rotating chamber.
- This core, or "bed," is filled with solid particles such as catalysts, adsorbents, or immobilized enzymes.
- As the bed rotates, it creates a centrifugal force that pushes the liquid outwards through the bed.
- This forced flow significantly enhances the contact between the liquid and the solid particles.
The result is a dramatic increase in mass transfer rates, leading to faster reactions, more efficient separations, and improved overall process performance. This unique design allows for easy scaling and adaptation to various chemical processes, making it a versatile solution for numerous industrial applications.
Biocatalysis
Biocatalysis refers to the use of natural catalysts, such as enzymes or whole cells, to perform chemical transformations on substrates, often to produce desired products in a more environmentally friendly and efficient manner compared to traditional chemical methods. This approach is widely used in industries like pharmaceuticals, biotechnology, and food processing.
Enzyme Technology Alliance
The Enzyme Technology Alliance (ETA) is a collaborative initiative that brings together leading experts and organizations in the field of enzyme technology. This alliance aims to accelerate innovation, share knowledge, and develop cutting-edge solutions in biocatalysis and enzyme engineering.
Key objectives of the ETA include:
- Fostering research and development in enzyme technology
- Promoting the adoption of sustainable biocatalytic processes in industry
- Facilitating knowledge transfer between academia and industry
- Developing standardized methods and best practices in enzyme technology
Through this alliance, we at SpinChem are able to leverage a vast network of expertise, enhancing our capabilities in biocatalysis and expanding the potential applications of our Rotating Bed Reactor technology in enzyme-based processes.
Collaborative Offerings
Together with our partners in the Enzyme Technology Alliance, SpinChem can offer clients a comprehensive suite of services and technologies:
- Enzyme Discovery and Engineering: Leveraging the bioinformatics, modeling, and AI-supported enzyme engineering capabilities of partners like Candidum, Aminoverse, and Allozymes.
- Biocatalyst Immobilization: Combining SpinChem's expertise in solid phase utilization with ChiralVision's 16 years of experience in designing immobilized enzyme processes.
- Process Development and Scale-up: Utilizing SpinChem's rotating bed reactor technology alongside the alliance's collective expertise in DOE-based process intensification and scale-up of enzyme production and chemo-enzymatic processes.
- Custom Solutions: Offering tailored solutions for diverse chemistry and API production, supported by the alliance's combined 150 years of experience in managing projects from enzyme discovery to cGMP enzymatic production of APIs.
Mass Transfer
Mass transfer in liquid-solid reactions is a crucial process in chemical engineering, particularly in heterogeneous systems. It involves the movement of molecules or ions from one phase to another, typically from a liquid bulk to a solid surface or vice versa. This transfer is essential for many industrial processes, including adsorption, ion exchange, and heterogeneous catalysis.
The efficiency of mass transfer significantly impacts the overall reaction rate and yield. Factors affecting mass transfer include:
- Surface area of the solid phase
- Concentration gradients
- Fluid dynamics (e.g., mixing and flow patterns)
- Physical properties of the liquid and solid phases
Enhancing mass transfer is a key focus in process optimization, as it can lead to faster reactions, improved product quality, and reduced energy consumption. Technologies like SpinChem's Rotating Bed Reactor are designed to address these challenges by creating optimal conditions for efficient mass transfer in liquid-solid systems.
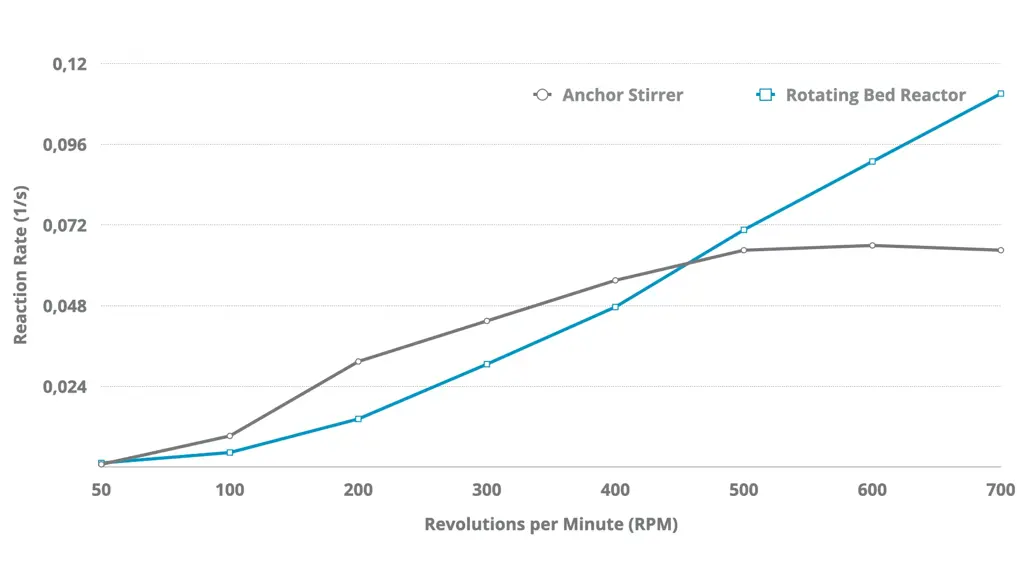
Key Observations:
1. Reaction Rate Increases with RPM:
For both systems, the reaction rate increases with RPM initially. This indicates improved mixing and mass transfer as the systems operate at higher speeds.
2. Performance of the Anchor Stirrer:
The Anchor Stirrer reaches a plateau in reaction rate around 500 RPM, suggesting that mass transfer limitations dominate beyond this point. Further increasing RPM does not significantly improve the reaction rate.
3. Performance of the Rotating Bed Reactor:
The Rotating Bed Reactor demonstrates a continuous increase in reaction rate across the full RPM range shown. This suggests it is less affected by mass transfer limitations, maintaining efficient mixing and transport at higher speeds.
4. Overall Comparison:
- At lower RPMs (50–200 RPM), the Anchor Stirrer slightly outperforms the Rotating Bed Reactor.
- At higher RPMs (300+ RPM), the Rotating Bed Reactor outperforms the Anchor Stirrer, particularly after the Anchor Stirrer's performance plateaus.